21CFR Part 11 | The Importance of Achieving Process Compliance for Your Facility
21CFR Part 11 | The Importance of Achieving Process Compliance for Your Facility
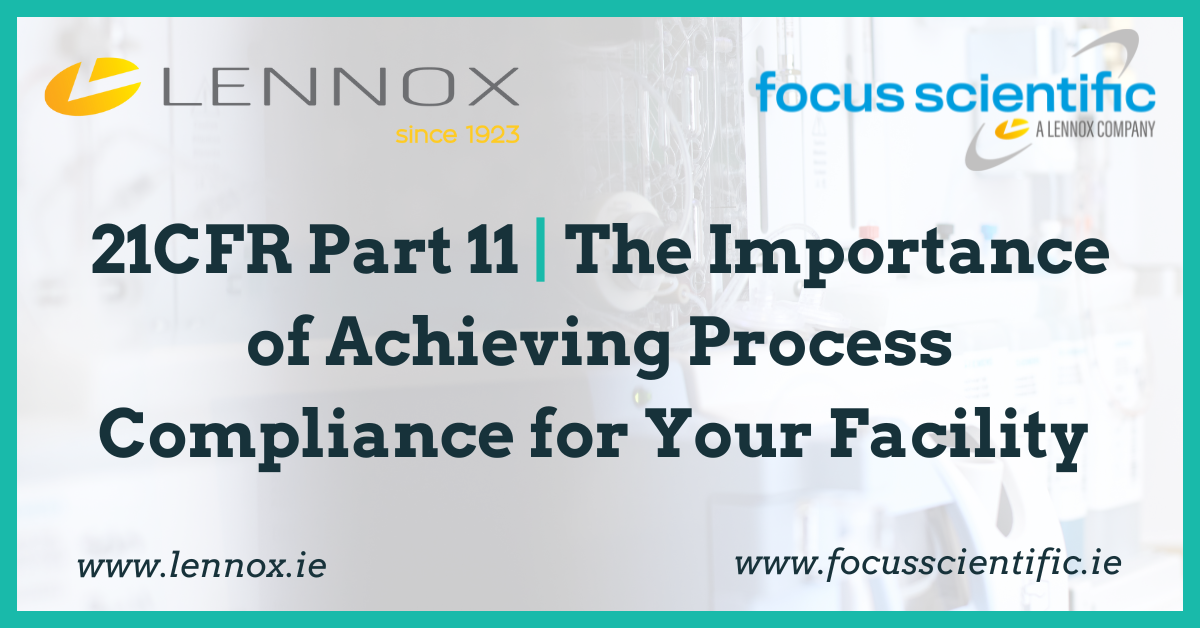
Process compliance in a manufacturing facility is the vital practice of adhering to cGMP (current good manufacturing practice) and procedures created to ensure a compliant operating environment. This set of controls covers aspects such as control of practices and procedures, data maintenance and security, integrity of computer-generated data, records and much more.
As specialist analytical equipment providers and an authorised distributor for USP-certified reference materials, Lennox and Focus Scientific Solutions understand how vital it is to maintain this very high level of industry compliance. In this blog, we will guide you through the importance of understanding and adhering to the 21 CFR Part 11 regulation, and how we can help ensure your facility has a 21 CFR Part 11 compliant system in place.
What is 21 CFR Part 11 and Why is it Important?
21 CFR Part 11 is a regulation which sets compliance standards for regulated industries to ensure electronic signatures and record-keeping processes are trustworthy and reliable. Companies in the pharmaceutical, biotechnology, medical device and similar industries are required to comply with these standards under the United States Food and Drug Administration (FDA) requirements. 21 CFR Part 11 is divided into subsections covering areas including system security, auditing, electronic signatures and access controls. By not adhering to this regulation, companies not only risk their reputation, but also being issued a 483, which requires detailing a “corrective action plan and then implement that corrective action plan expeditiously.” If they do not adhere, companies can be asked to cease production immediately.
Due to the risk of fraud or accidental damage in the process when completing critical documentation, this regulation was introduced to improve the quality and efficiency of record-keeping processes. The use of electronic records allows manufacturers to store data securely, ensuring the data is legitimate and in a format that cannot be altered, amended or deleted. The use of multiple server locations and cloud-based backups ensure safe storage and access of data for any audits required. Adhering to FDA and all other relevant compendia regulations will also ensure your facility can provide sale of products to the United States, and other regulated environments which can be lucrative markets for your industry.
Importance and Benefits of Compliance in a Regulated Industry
Whether it’s maintaining positive reputation or improving business processes, there are many benefits of being a compliant manufacturing facility. Adhering to industry standards and being compliant will help your facility be law-abiding and allow the continuation of production of your products worldwide.
Improved Reputation
A company that is known for adhering to regulations, demonstrates reliability and integrity externally, to customers, potential funders and suppliers, and internally, to their employees. Research shows that the public have little patience for companies who are not compliant and negative perception can affect your company’s reputation. This can have a ripple effect, affecting the views of stakeholders or other industry members and even your bottom line, so it is important to be honest and transparent and, most critically, law-abiding.
Legal Protection
It is important that you do all you can to protect your customers, your employees, who are depending on an income and the company, who are depending on you as a source of quality product. Non-compliance or fraudulent activity can also lead to injuries as well as fines, penalties and legal action including the risk of criminal prosecution.
Improved Processes Efficiency
Adhering to regulations such as Part 11 helps your company to effectively manage its operations. Efficient processes can lead to fewer human errors, ensuring a right first-time ethos where quality excels. All tasks are completed in a timely manner and in a controlled and secure method.
Ensure Your Manufacturing Systems Are Compliant Now
When identifying tenders or potential partners for your business, it is important to find someone that you can trust and who adheres to the proper industry compliance standards. When you choose Lennox and Focus Scientific, you are ensuring that your company will be working with a company that is aware of what is needed to meet industry requirements for all of your equipment and instrumentation.
Our factory trained Technical Sales Engineers will visit your site and discuss equipment specifications, installation, operational and performance qualification documentation. Our team will also provide you with tailored quotations for this analytical equipment, helping to ensure you and your team are fully compliant at every stage.
If you would like to learn more or require further information on our equipment portfolio or services, please contact: liam.coughlan@focusscientific.ie or visit www.lennox.ie and www.focusscientific.ie.